当今电子PCBA硬件终端客户对包工包料的需求日益强烈,传统PCBA厂家由于供应能力弱、价格无优势、货源不稳定、人工效率低,导致转化率低,面临客户越来越少、利润越来越薄的困扰。
然而制造终端工厂在选择PCBA代工代料过程中,又面临难以确认物料的真实性、PCB采购周期不稳定、电子元器件失效、维修困难、资金风险等难题。 那么在PCBA装焊过程中出现的MLCC失效问题,该如何解决及检测方法进行归纳总结,从优化生产工艺和设计改进着手,最终实现MLCC的高可靠性装焊? MLCC(片状多层陶瓷电容)其内部由多个电容错位叠压而成,简称MLCC,其具有体积小、单位体积电容量大、受温度等环境因素对性能影响小等优点,在军用通讯、雷达、炮弹引信、航空、航天、武器系统等领域被广泛应用。
MLCC现在已经成为了电子电路最常用的元件之一。MLCC表面看来,非常简单,可是在很多情况下,设计工程师或生产、工艺人员对MLCC的认识却有不足的地方。
有些公司在MLCC的应用上也会有一些误区,以为MLCC是很简单的元件,所以工艺要求不高。其实,MLCC是很脆弱的元件,应用时一定要注意。 分类汇总:介质击穿、开路、电参数变化(电容量超差、损耗角正切值增大、绝缘电阻下降或漏电流上升等)、引线腐蚀或断裂、绝缘子破裂或表面飞弧等。■ 钽电解电容器:电压过载击穿烧毁;浪涌电压冲击漏电流增大;极性反向短路;高温降额不足失效;■ 铝电解电容器:漏电流增大击穿;极性反向短路;高温降额不足失效;■ 有机薄膜电容器:热冲击失效;寄生电感过大影响高频电路功能实现;■ MLCC(2类):SMT工艺不当导致断裂或绝缘失效;Y5V温度特性不佳导致电路故障;引起MLCC失效的原因多种多样,各种MLCC的材料、结构、制造工艺、性能和使用环境不相同,失效机理也不一样。 通过对过往失效样品分析可知,常见的失效机理有:内部分层、介质缺陷、金属离子迁移、介电老化等。同一失效模式有多种失效机理,同一失效机理可产生多种失效模式,两者并非一一对应的。
随着技术的不断发展,贴片电容MLCC现在已可以做到几百层甚至上千层了,每层是微米级的厚度,所以稍微有点形变就容易使其产生裂纹。另外同样材质、尺寸和耐压下的贴片电容MLCC,容量越高,层数就越多,每层也越薄越容易断裂。 另外一个方面是,相同材质、容量和耐压时,尺寸小的电容要求每层介质更薄,导致更容易断裂。
裂纹的危害是漏电,严重时引起内部层间错位短路等安全问题。而且裂纹有一个很麻烦的问题是,有时比较隐蔽,在电子设备出厂检验时可能发现不了,到了客户端才正式暴露出来。所以防止贴片电容MLCC产生裂纹意义重大。
在产品正常使用情况下,失效的根本原因是MLCC 外部或内部存在如开裂、孔洞、分层等各种微观缺陷。这些缺陷直接影响到MLCC产品的电性能、可靠性,给产品质量带来严重的隐患。 主要由于器件在焊接特别是波峰焊时承受温度冲击所致,不当返修也是导致温度冲击裂纹的重要原因。 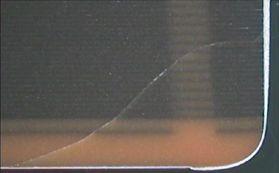
当贴片电容MLCC受到温度冲击时,容易从焊端开始产生裂纹。在这点上,小尺寸电容比大尺寸电容相对来说会好一点,其原理就是大尺寸的电容导热没这么快到达整个电容,于是电容本体的不同点的温差大,所以膨胀大小不同,从而产生应力。这个道理和倒入开水时厚的玻璃杯比薄玻璃杯更容易破裂一样。 另外,在贴片电容MLCC焊接过后的冷却过程中,贴片电容MLCC和PCB的膨胀系数不同,于是产生应力,导致裂纹。要避免这个问题,回流焊时需要有良好的焊接温度曲线。如果不用回流焊而用波峰焊,那么这种失效会大大增加。 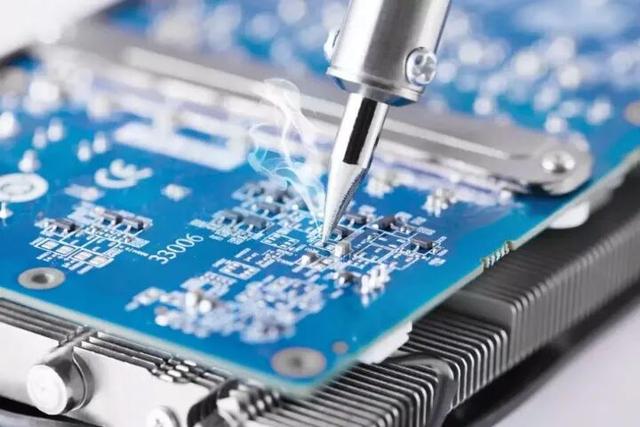
MLCC更是要避免用烙铁手工焊接的工艺。然而事情总是没有那么理想。烙铁手工焊接有时也不可避免。 比如说,对于PCB外发加工的电子厂家,有的产品量特少,贴片外协厂家不愿意接这种单时,只能手工焊接;样品生产时,一般也是手工焊接;特殊情况返工或补焊时,必须手工焊接;修理工修理电容时,也是手工焊接。无法避免地要手工焊接MLCC时,就要非常重视焊接工艺。 MLCC多层陶瓷电容器的特点是能够承受较大的压应力,但抗弯曲能力比较差。器件组装过程中任何可能产生弯曲形变的操作都可能导致器件开裂。 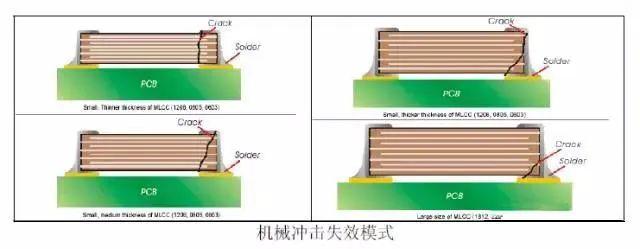 - 电路测试、PCBA板分割(v-cut or 铣刀分板);该类裂纹一般起源于器件上下金属化端,沿45℃角向器件内部扩展。该类缺陷也是实际发生最多的一种类型缺陷。 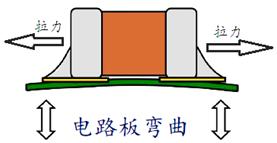 ② 超过PCB 的弯曲度及对PCB 的破裂式冲击;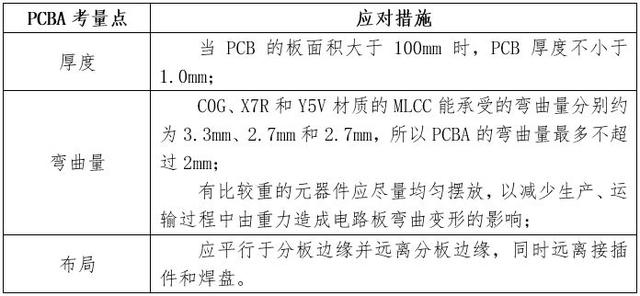 ③ 吸嘴贴装(贴装吸嘴下压压力过大及下压距离过深)及定中爪固定造成冲击;产品在电路板贴装时,不应该受到过大的冲击,必须定期对吸头和定位爪进行检查、维修和更换。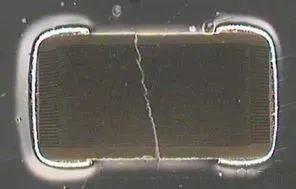
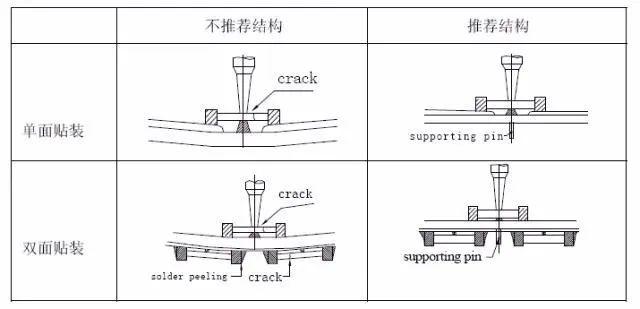 ⑤ 手工焊接环节:焊接过程烙铁头或防静电镊子按压器件本体、器件两端头焊锡量过多或不均匀,可造成开裂,见图8。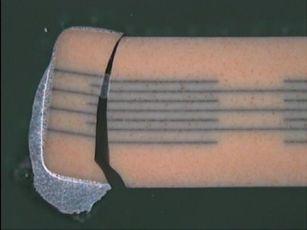 ⑥ 印制板清洗环节:手工清洗用力过大、清洗方法错误或清洗刷头过硬,可造成开裂;若器件在前工序已造成了内部裂纹存在,则MLCC在清洗工序中可能造成电极和陶瓷本体脱落的现象。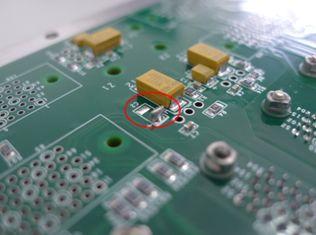
MLCC 的陶瓷体是一种脆性材料。如果PCB 板受到弯曲时,它会受到一定的机械应力冲击。当应力超过MLCC 的瓷体强度时,弯曲裂纹就会出现。因此,这种弯曲造成的裂纹只出现在焊接之后。 ① PCB 板弯曲时在不同位置受到的应力大小不同:元件装配接近PCBA分板点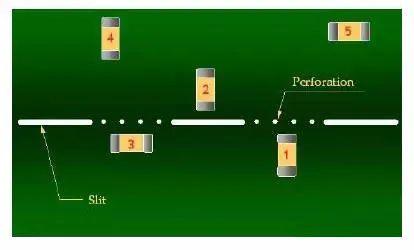
② PCB 板弯曲导致的开裂(产品摆放方向):开裂产生于产品接近或者垂直于分板线③ 焊锡量过多引起PCB 板弯曲导致开裂:过多的焊锡量导致空洞产生的主要因素为陶瓷粉料内的有机或无机污染,烧结过程控制不当等。空洞的产生极易导致漏电,而漏电又导致器件内部局部发热,进一步降低陶瓷介质的绝缘性能从而导致漏电增加。该过程循环发生,不断恶化,严重时导致多层陶瓷电容器开裂、爆炸,甚至燃烧等严重后果。 烧结裂纹常起源于一端电极,沿垂直方向扩展。主要原因与烧结过程中的冷却速度有关,裂纹和危害与空洞相仿。 多层陶瓷电容器(MLCC)的烧结为多层材料堆叠共烧。烧结温度可以高达1000℃以上。层间结合力不强,烧结过程中内部污染物挥发,烧结工艺控制不当都可能导致分层的发生。分层和空洞、裂纹的危害相仿,为重要的多层陶瓷电容器内在缺陷。 工艺方法选择上应多考虑MLCC的温度特性和尺寸,避免热应力造成的缺陷。比如1210以上的大尺寸MLCC,在选择焊接工序时,不宜采用波峰焊接,因为大尺寸的电容导热设计不如小尺寸,容易造成电容受热不均匀,从而产生破坏性应力。
而一但焊接方法确定为波峰焊接或回流焊接时,应注意焊接设备的温度曲线设置,温度曲线应由授权的工艺技术人员负责设定,验证、修改和发布;参数设置中跳跃温度不能大于150℃,温度变化不能大于2℃/秒,预热时间应大于2分钟以上,焊接完毕不能采取辅助降温设备,应自然随炉温冷却。 连接器附近加装滤波电容,进行连接器插拔时,若连接器周围没有板面支撑设计,PCB板产生翘曲变形也可导致附近的器件产生裂纹,因此可考虑在连接器周围增加安装孔或垫柱设计,以减少插拔过程印制板的变形。
其次,从工艺设计流程上进行优化,通过制作托盘工装,将丝网印刷→表面贴装→回流焊接→裁板这种工艺流程改为表贴喷印→表面贴装→回流焊接工艺流程,以托盘工装为载体连接各小板,可省去拼板后再裁板的工步,下图为某产品使用托盘工装后的效果图。 对于外部缺陷,通常采用显微镜下人工目测法或自动外观分选设备。而内部微小缺陷一直是MLCC检测的难点之一,它严重影响到产品的可靠性,却又难以发现。超声波探伤方法能够更精确地检测出MLCC内部的缺陷,从而分选出不良品,提高MLCC的击穿电压与高压可靠性。
关于超声波探伤仪 - 利用超声波的穿透与反射(表面波和底波)的特性来检测物体中的缺陷。采用超声波探伤仪能准确地找出有缺陷的MLCC 产内部微缺陷,并且能够确定缺陷的位置,进一步的磨片分析,对于发现有内部缺陷的产品则采用整批报废处理,表明了超声波探伤方法在MLCC内部缺陷的检测、判定上的有效性与可靠性。
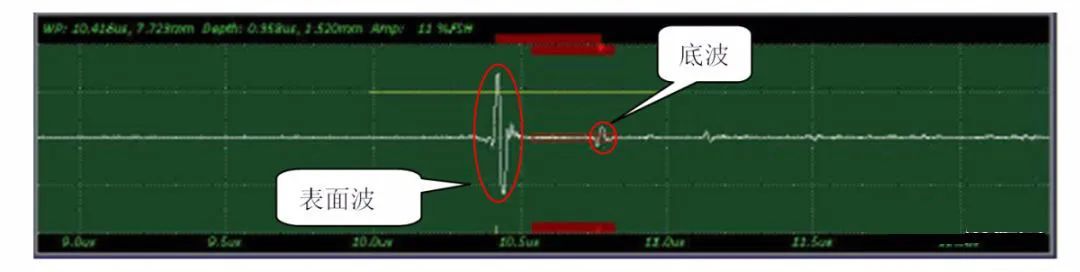
正常样品:样品扫描照片整体颜色为绿黄色,表示样品本体显示正常。部分样品边缘出现红蓝色,是由于样品边缘表面高度不均匀造成,属于正常现象。
异常样品:样品本体颜色会出现红蓝色,则会再次对可疑样品进行扫描确认。

超声波扫描后的样品成像如图
其他元器件及IC产品失效分析 - 不止MLCC失效分析,还可以对其他电子元器件及IC产品进行失效分析。电子元器件失效分析对产品的生产和使用都具有重要的意义,通过分析工艺废次品、早期失效、试验失效、中试失效以及现场失效的样品,确认失效模式、分析失效机理,明确失效原因,最终给出预防对策,减少或避免失效的再次发生。
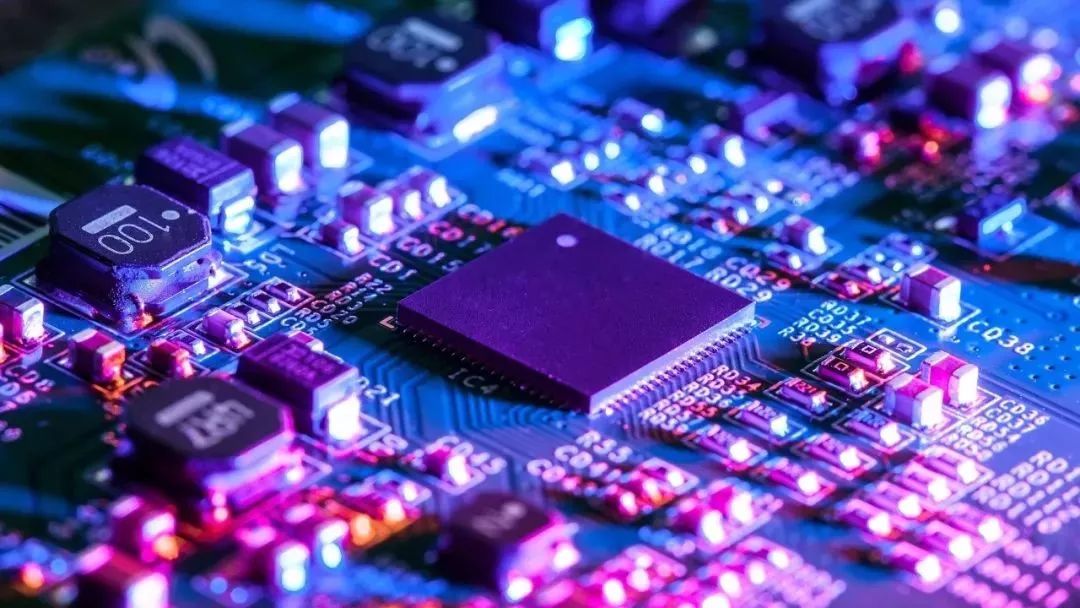
常见的IC失效模式 失效模式:静电损伤、金属电迁移、芯片粘结失效、过电应力损失、金属疲劳、热应力、电迁移失效、物理损伤失效、塑料封装失效、引线键合失效。
失效检测分析方法: 目的是通过掌握样品电参数或功能失效状况,方便为进一步分析作准备。观察量测:通过观察IC外部/内部外观&结构,确认IC异常位置及具体状况。该类测试一般与DPA(即破坏性物理分析)结合使用。 DPA破坏性测试:通过液体侵蚀、机械破坏、激光切割等破坏方式,对IC内部具体失效位置进行定位及呈现。可靠度测试:是通过使用各种环境试验设备,模拟气候环境中的高温、低温、高温高湿以及温度变化等情况,验证IC寿命及性能稳定性。MLCC属于新型电子元器件,是电子信息产品不可或缺的基本组件之一;它在各类军用、民用电子产品的多种电路中被广泛应用。
因此,MLCC的装焊质量控制显得尤为重要,所以产品的可靠性不仅是设计出来的,也是生产出来的,而检验只能验证产品的可靠性,不能提高产品的可靠性;从产品设计、生产工艺、过程管控三管齐下,才是实现高可靠MLCC装焊的三个基本途径。 |